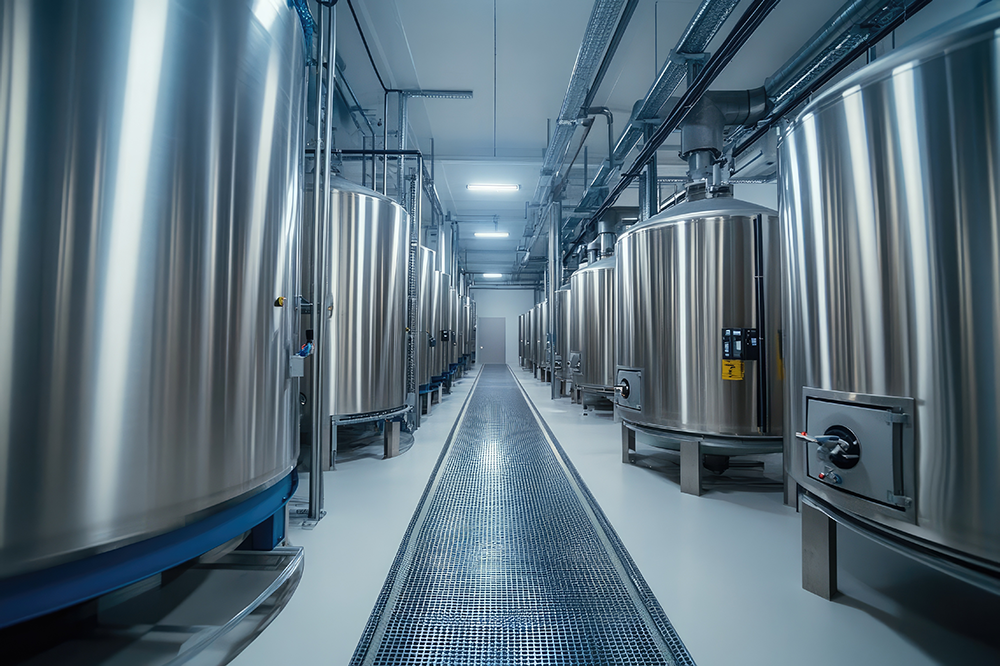
I livsmedels- och läkemedelsindustrin är det avgörande att produktionen sker med högsta möjliga hygien, säkerhet och processkontroll. En ofta underskattad men helt avgörande komponent i dessa processer är ventilen. Ventiler styr flöden, förhindrar korskontaminering och möjliggör effektiv rengöring, utan att produktionen behöver stoppas.
I detta inlägg går vi igenom tre vanliga ventiltyper i hygieniskt utförande och hur innovativa lösningar som Mix-Proof ventiler, sätesventiler och vridspjällsventiler från vår partner GEA kan bidrar till en trygg och effektiv processhantering.
GEA Mix-Proof ventiler – maximal säkerhet och effektivitet
GEA Mix-Proof ventiler, även kallade dubbelsätesventiler, är utformade för att hantera två olika vätskor samtidigt, helt utan risk för korskontaminering. Det gör dem särskilt värdefulla i miljöer där produkter och rengöringsmedier måste hållas åtskilda, exempelvis inom mejeri, bryggeri och läkemedelsproduktion.
GEA var först på marknaden med att utveckla och lansera den unika Mix-Proof-tekniken – en innovation som har satt standarden i branschen.
Tack vare den dubbla tätningen med integrerad läckagedetektion kan en del av systemet rengöras (CIP) medan produktionen fortsätter i en annan del, vilket ökar anläggningens flexibilitet och driftstid.
Nedan har vi sammanfattat några av de största fördelarna med GEA:s Mix-Proof ventiler:
- Dubbel tätning med läckagedetektering – för maximal säkerhet och hygien
- CIP under pågående produktion – spara tid och öka kapaciteten
- Automatiserad, hållbar konstruktion – för lång livslängd och driftsäkerhet
- LEFF (Low Emission Flip-Flop) – minskar CIP-förbrukningen med upp till 90 %, ger ökad rengöringseffekt och sänker kemikalieåtgången
- Hög processäkerhet – för tillförlitliga och säkra produktionsflöden
Detta gör Mix-Proof ventiler till ett självklart val när både produktsäkerhet och produktionsflexibilitet behöver prioriteras samtidigt.
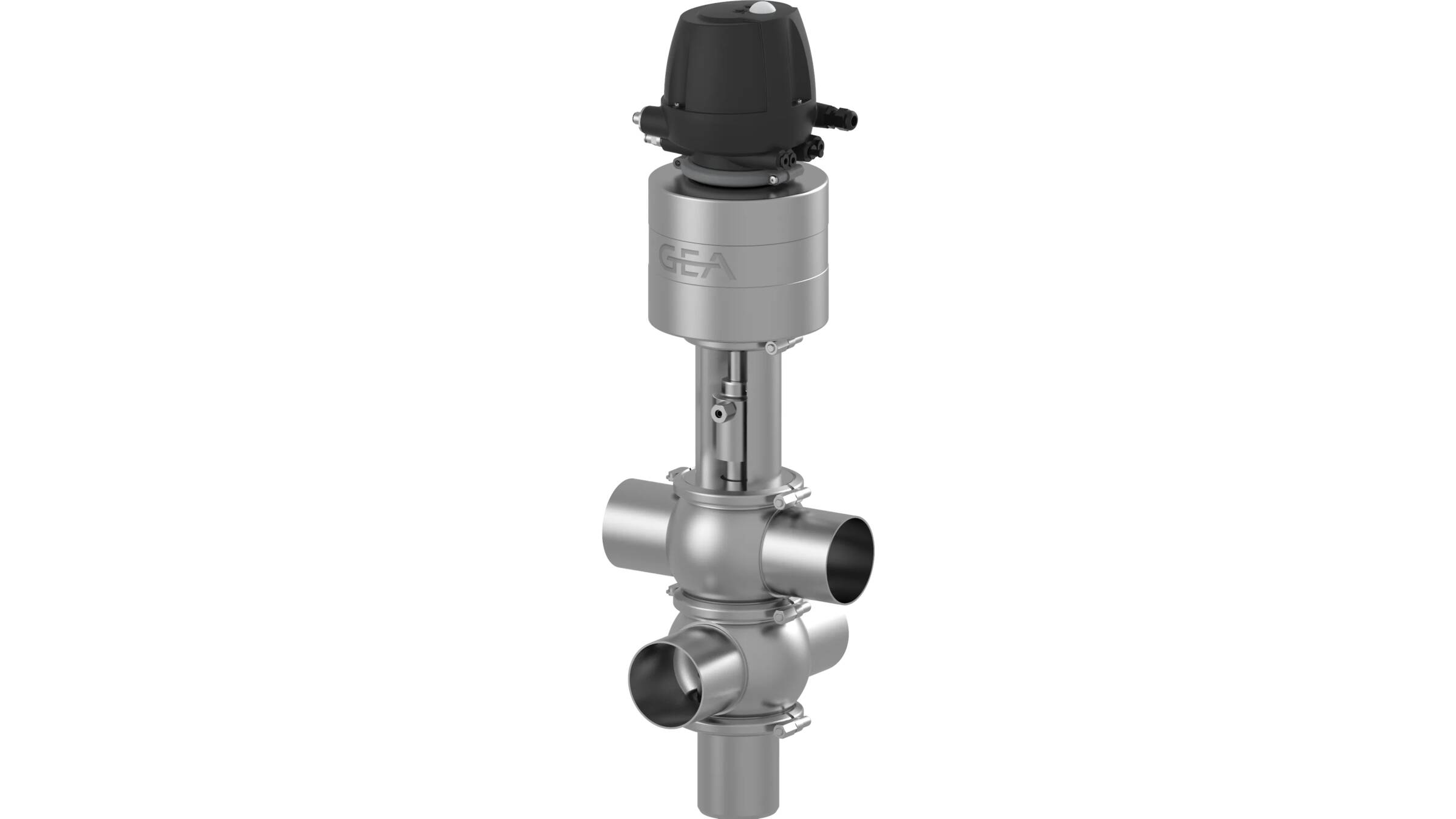
Sätesventiler – hygieniska ventiler för flexibel flödeskontroll
När behovet av hygienisk flödeskontroll är högt men processerna inte kräver samtidig hantering av flera vätskor såsom i mix-proof-lösningar, är sätesventilen ett smart och kostnadseffektivt val.
Den vertikala öppnings- och stängningsmekanismen gör den perfekt för allt från produktväxling mellan linjer till rengöring och sterilisering på plats (CIP och SIP). Dessutom finns sätesventiler i både enkelsätes- och dubbelsätesutföranden för att matcha olika systemkrav. Detta leder till en lösning som är både tillförlitlig och lätt att underhålla – särskilt i applikationer där enkelhet, hygien och lång livslängd står i fokus.
Här är några av de egenskaper som gör GEA:s sätesventiler till ett uppskattat val:
- Hygienisk design med minimala döda zoner – för säker och kontrollerad drift
- Enkla att underhålla – med slitstarka tätningar som ger lång livslängd
- Tillförlitliga i drift – även under krävande processförhållanden
- Flexibla konfigurationer – ett brett utbud av modeller för olika applikationer
GEA:s sätesventiler är det självklara valet för hygienkritiska processer där kvalitet, effektivitet och flexibilitet är i fokus.
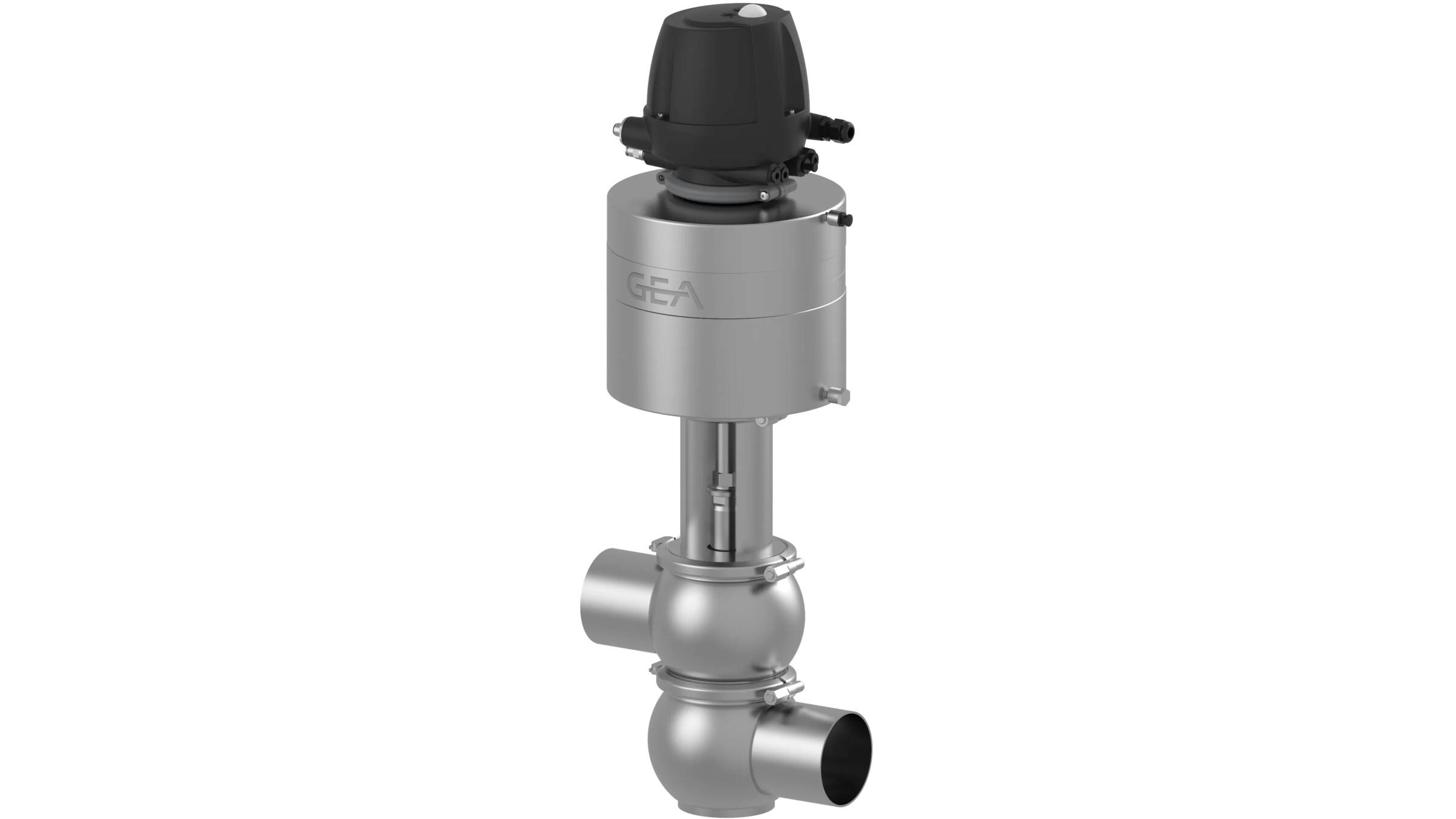
Vridspjällsventiler – kompakta ventiler för hygienisk avstängning
När behovet är att snabbt och pålitligt kunna stoppa ett flöde, till exempel för att växla produktlinje eller isolera en del av systemet – erbjuder vridspjällsventilen en enkel och effektiv lösning. Den används ofta där exakt flödesreglering inte krävs, men där hygien, täthet och funktionalitet fortfarande är avgörande.
Tack vare sin kompakta design och låga vikt är den särskilt populär i stödprocesser, exempelvis för att stänga av flödet av vatten, luft eller CIP-vätskor (rengöringsmedier som används i CIP-processer).
Nedan har vi sammanfattat varför denna ventiltyp är ett uppskattat val i hygieniska system:
- Enkel att installera och kräver minimalt underhåll
- Lämplig för mindre kritiska medier som vatten, luft och rengöringsvätskor
- Kostnadseffektiv lösning i stödprocesser
- God tätning tack vare hygieniskt anpassade tätmaterial
Detta gör vridspjällsventilen till en praktisk komponent i alla system där driftsäkerhet, renlighet och enkel hantering går hand i hand.
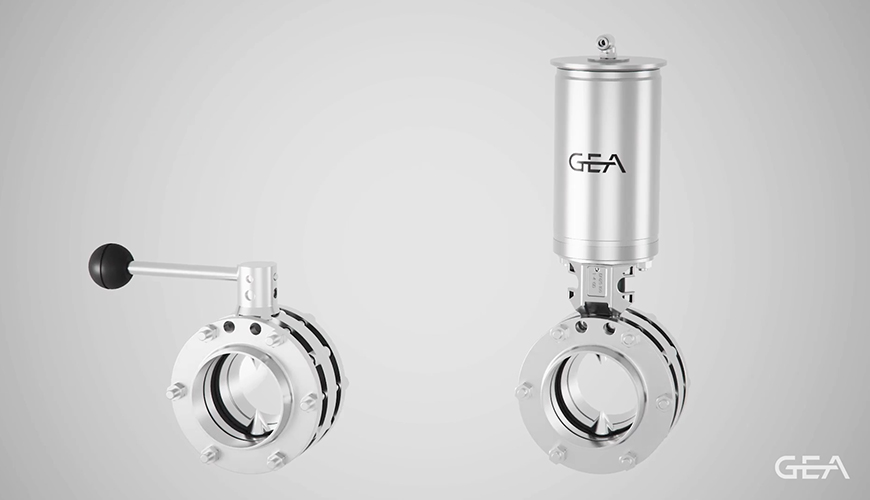
En helhetslösning för hygieniska processer
Att välja rätt ventil i hygieniska processmiljöer är avgörande – inte bara för produktkvaliteten, utan för hela anläggningens effektivitet, driftsäkerhet och rengöringsbarhet. Genom att kombinera olika ventiltyper utifrån deras specifika styrkor kan du bygga system som klarar både dagens processkrav och framtidens förändringar.
På Colly Flowtech ser vi till helheten. Genom vårt partnerskap med GEA erbjuder vi inte bara ett komplett ventilprogram, utan även teknisk rådgivning och lösningar för effektiv CIP-rengöring, inklusive statiska och roterande spraykulor.
Vill du veta mer om hur rätt ventilval kan förbättra din produktion? Tveka inte att höra av dig – vi delar gärna med oss av vår erfarenhet.
Denna text är skriven av Morgan Malm (morgan.malm@colly.se), Försäljningschef på Colly Flowtech.
Här hittar du vårt produktutbud från GEAVanliga frågor om ventiler
Varför är ventiler viktiga inom livsmedels- och läkemedelsproduktion?
De styr flödet av vätskor och gaser i hygieniska processlinjer. Ventilerna säkerställer att produktionen sker kontrollerat, säkert och utan kontaminering.
Vilken ventiltyp används oftast inom hygieniska processer?
Sätenventiler och membranventiler är vanligast eftersom de är lätta att rengöra. De uppfyller också strikta hygienkrav för både livsmedel och läkemedel.
Varför ställs så höga krav på ventilernas utformning?
För att förhindra bakterietillväxt och produktförorening. Ventilens design påverkar både produktkvalitet och efterlevnad av branschstandarder.
Hur säkerställs rengöring av ventiler i produktionen?
Med CIP- och SIP-system rengörs ventiler automatiskt utan att monteras isär. Det minskar risken för mänskliga fel och sparar tid.
Vilka material används i ventiler för livsmedels- och läkemedelsproduktion?
Rostfritt stål, särskilt 316L, är vanligt på grund av dess korrosionsbeständighet och hygieniska egenskaper. Tätningar är ofta gjorda av material som EPDM eller PTFE för att tåla CIP/SIP-processer.
Författare
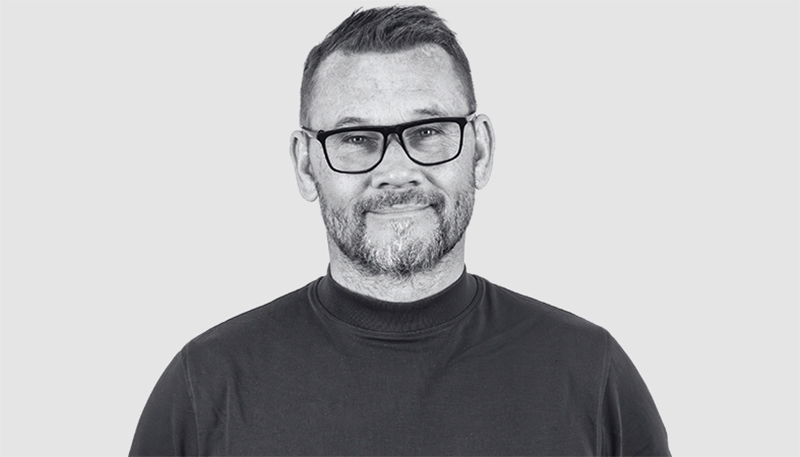